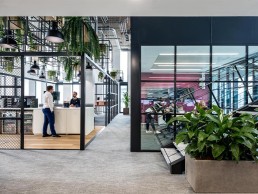
GreenLight Alliance: An Architectural Perspective
Perkins + Will Sustainability Director Dr. Asif Din, alongside Associate Erik Svensson, offer an outsider’s view on how the circular economy fits within the wider design approach.
At Perkins&Will, we have always been looking at the environmental impact of our projects. We are an architectural practice based in London, part of a larger worldwide company, working at a range of differing scales from masterplanning to corporate interiors. The more we quantified the impact of corporate fit outs, we found the impact was larger than first thought. This is due to the fit out of buildings being a continuous cycle of environmental impact, which eclipses the building envelope over its lifespan. We looked closely at a designer’s input and the influence we have in terms of design and specification of our projects.
Our design responsibilities are extending beyond sustainability to a circular economy mechanism to meet 2050 carbon targets. We cannot delay in providing a methodology on how this would be achieved and act immediately.
The impetus is not solely from a designers’ standpoint; there are a range of client requirements that are emerging. The concept of corporate extended responsibility requires all corporations to conduct themselves correctly, looking at their whole supply chain. Much of the funding they receive is increasingly tied to environmental indicators. Corporations are also increasingly declaring their carbon emissions with commitments to use completely renewable energy, roadmaps to zero carbon and the payments of offsets through verified methodologies such as science-based targets.
We believe that offsets should be used as a last resort to meeting carbon commitments and designers have the remit to minimise carbon within the real estate sector. There is a limited resource of offsetting that corporations can access. To reduce carbon at the earliest stage of the design that has the potential for the largest reduction of carbon.
To achieve this vision, we had to set our own roadmap. This included a commitment on transparency and reporting stages to the industry to communicate the successes but also where the gaps and failings are to achieve our milestones. A net zero carbon interior is not possible now and will require effort from the whole supply chain to achieve our 2030 target date to systemically change the way we deliver interior projects.
Our roadmap outlines a series of focus areas. While we cannot currently design a fully circular project, we can make at least one or a few areas on each project circular. The knowledge gained from each project will move us towards designing complete circular projects. This would be achieved through:
1. Sourcing materials with Environmental Product Declarations (EPDs) and/or Health Product Declarations (HPDs) supporting transparency and engaging with smaller manufacturers developing new sustainable materials.
2. Design for disassembly: consider how each component is put together and how it can be taken apart to be reused in the future.
3. Undertake a Life Cycle Analysis during the earlier stages of the design process to evaluate and highlight opportunities to reduce the project impact. This should be considered an iterative process that continues on site in collaboration with the contractor.
The incremental targets set along the timeline include processes, training, and specification changes to achieve goals. This not only effects how we design but what we design as the aesthetics move towards concepts that favour honesty of materials and how things are fitted together.
Using a Life Cycle Analysis (LCA) is the most transparent methodology to quantify where we are in the journey to achieving a net zero carbon interior. This, like any other construction project, is large in its initial amount and then decreases over the lifespan of the project. However, as the cycles are short with interiors projects, this spike occurs at a more frequent basis. Using Greenhouse Gas Emission impacts (GHG) allows us to show the impact of a range of chemicals and potentially allows the comparison of projects to take place in the future.
However, the scope of GHG quantification is limited to the closed system boundary of the site and its materials. To reduce impacts on a larger systemic level the principles of the Circular Economy (CE) are used. There are no established metrics for circularity, but a LCA impact assessment is a good fit. During the lifetime of a product, GHG reduction can be demonstrated through reuse, manufacturing of goods using different and less raw material, eliminating waste and the need to recycle at the end of the product’s life, and to increase longevity, creating a secondary market for the product.
The reality is that it is often easier and more cost effective to dispose of existing materials on project site and source all new. This is one of the many barriers our industry needs to overcome.
If the long-term goal is fully circular, there must be an invested interest from the manufacturers to receive their products back. In current design process the industry is ill prepared for circularity as purchasing reconditioned materials raises concerns, particularly around warranties. There is also often a perception of the concepts of second hand, reused or reconditioned items that must be overcome.
There are products already in the market that are moving towards a circular ethos. A good example is that of a European carpet manufacturer who offer full transparency on the list of all the ingredients that they use. They have operated a takeback service aligning with extended manufacturer responsibilities for several years but in addition have a Materials as a Service offering where the flooring is leased.
Within their manufacturing their product is fully recyclable, and they are increasing their recycled content as the feedstock from old product allows. They are only able to control this process through the ownership of their own recycling facility disassembling product to provide feedstock to mills to be made into new yarn.
We are currently working on a project in London; with the full project teams’ goals on sustainability aligning, the project is an opportunity to explore and continuously find opportunities to drive change in the industry. The project focused on circularity and going beyond sustainability accreditations from the start, creating a strong framework for the client and project team to work towards.
The project is in a previously occupied building, giving the project team a set of materials and components already installed. Repurposing elements from the previous fit out offers potential cost saving and innovative opportunities. Some are less glamorous, such as reconfiguring existing WCs rather than demolishing and installing new, whilst others can be part of a project storytelling, such as repurposing the timber from existing door frames to create handrails for new staircases.
Sourcing furniture in a more circular way, by focusing on remanufactured and reused furniture, aims to drive a much-needed shift in the furniture industry away from a linear model. According to Eramus+ (2017) approximately 80-90% of discarded furniture goes to landfill, many designed to last far longer than a typical office lease period.
Considering each material that goes into the new project can make a significant impact. For example, reducing the amount of metal used in the project by installing a glulam staircase. Each component change may not be significant in impact, but in combination creates a large difference. When we do the final LCA at the end of the project we will evaluate what we have achieved and take these learnings to the next project.
This is a journey in which we are now gaining the knowledge and clear direction to achieving a net zero carbon interior in the future. From this process we have learnt that we can only assess progress if there is a defined methodology involved. Although an LCA does not fully include CE, it does provide a good fit to the main aims of carbon reduction in interiors projects. We have discovered splitting of technical and biological components as much as possible allows better quantification and end of life processes to be made. This will require a designer mindset shift to viewing the building as a temporary material store rather than the end of the material journey occurring at hand over.
This cannot be achieved by us alone and requires the whole industry to similarly examine and deliver products in a similar light. We need transparency of material ingredients as it is the feedstock of the future building components. We need to eliminate waste through all stages of production and allow dismantling of components to be reused. This will require manufacturers to no longer view new product as a primary source of income but the responsibility of maintenance and repair to elongate life, making refurbished components the equivalent of new. This can only occur if this process is less arduous than the current practice of placing all components into a mixed recycling skip at the end of a lease period in an office fit out.
The most efficient way of reducing embodied carbon is to not install the component to start with. As designers we need to ask ourselves what the purpose of each component is, and if it really needs to be there. Whilst currently this puts restraints on the design, the industry is and will keep changing.
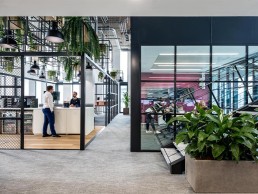