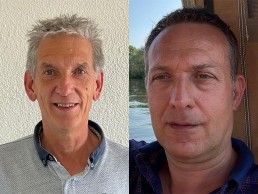
GreenLight Alliance: TM65: a driver manufacturer’s perspective
Rob Bremmert, Quality Engineer and Patrick van der Meulen, Business Development Manager at eldoLED, break down CIBSE’s TM65 initiative, and explain what it means for driver manufacturers.
The global building industry’s response to national net-zero carbon targets will be a big factor in determining whether humanity avoids a catastrophic climate crisis in the coming decades.
Figures for the UK published by the UK Green Building Council (UKGBC) show that the built environment is responsible for more than 25% of total UK greenhouse gas (GHG) emissions. Annual emissions from the building sector have fallen by around 30% since the turn of the century, but this is largely attributable to the growth in renewables, mostly wind and solar, as a proportion of total electricity generation. In other words, it is not the result of any specific initiative for which the building sector can take credit, but is largely the result of government policy for the electricity industry.
Nevertheless, this means that operational emissions – to heat and light buildings and to power appliances – are on a downward trajectory. Harder to reduce are the embodied carbon emissions generated by the production of building materials and appliances, by the construction process itself, and by the disposal and decommissioning of equipment and structures. But without a massive reduction in embodied carbon emissions, the building sector has no chance of reaching net zero.
The first step in reducing the carbon built into new construction projects, refurbished, or re-equipped buildings, is to understand how much embodied GHG, measured in equivalent kilograms of carbon dioxide (kgCO2e), is in the various components of a building project.
This is why the TM65 initiative from CIBSE has attracted the attention of environmentally aware individuals and organisations in the lighting industry, not only in the UK, but around the world: for the first time it gives lighting designers, specifiers and architects a clear and transparent way to calculate the carbon embodied in new lighting equipment.
So what is the purpose of the TM65 standard? How is embodied carbon calculated according to TM65? And what is the experience of performing TM65 calculations for a manufacturer of lighting equipment?
TM65 explained
The embodied carbon in a product is the GHG emissions associated with the extraction of the materials from which the product is assembled, its manufacturing process, repair, and treatment at the product’s end of life, as well as any GHG produced in the shipping of the product. TM65 can be carried out at a basic level (where stages A2, A3, A4, C2, C3 and C4 are simply scaled via a buffer factor (fig. 1) or at mid-level where they are individually accounted for.
To illustrate the point, let’s use the example of an LED driver, since this is eldoLED’s area of expertise.
The global warming potential embodied in an LED driver arises from the materials that it contains, such as copper, aluminium, brass and plastic. Energy is required to mine, process, and refine the raw materials, to shape them, then to transport them to the factory where they are assembled into a new LED driver. At the end of a luminaire’s life, the materials in the driver will be transported to a waste treatment site, where they will be either buried in landfill, or better, recycled. Every part of this process uses energy, and so generates GHGs.
The total GHG emissions attributable to a product can be declared in an environmental product declaration (EPD), having executed an exhaustive LCA (Lifetime Carbon Assessment). A full LCA verified into a legitimate EPD is time consuming and expensive, hence, very few building services equipment manufacturers offer them.
This is why CIBSE devised TM65, a toolkit to enable consultants or designers to calculate the embodied carbon associated with mechanical, electrical and public health (MEP) systems in buildings when no EPD is available. Lighting professionals can use TM65 calculations to build a reliable estimate of the global warming potential of a lighting scheme early in the design phase. With the information provided by TM65, the industry can make informed choices to reduce the carbon embodied in the lighting equipment installed in new or refurbished buildings.
Weighing and measuring: what it takes to perform a TM65 calculation
The basic method of calculating a TM65 embodied carbon value has four stages (ignoring refrigerants. See Figure 1). It starts with an analysis of the components of a product. The product’s manufacturer will:
· Break down a product into its basic materials, such as various metals, plastics, rubber, and in the case of an LED driver, electronic components and the PCB.
· Weigh each material separately, up to at least 95% of the total product weight.
· Apply an embodied carbon coefficient to each material. The coefficients are provided in the TM65 specification. The sum of these gives subtotal 1 (fig.3).
In the second stage, subtotal 2 incorporates a repair allowance. During a product’s life, it might be repaired. TM65 adds a step after the initial calculation to allow for the embodied carbon in parts that are typically replaced before a product reaches the end of its life. In the absence of specific information about replacement, it is assumed that 10% of the weight of a product will be replaced during its life (fig. 3).
The third stage is to apply a ‘scale up factor’: this takes account of the carbon embodied in the processes of shipping, assembling, decommissioning and disposing of a product. The scale up factor is lower for simple products and higher for complex products: for an LED driver, the scale up factor is x1.4 and is applied to the total embodied carbon value for the manufactured and repaired product. (see subtotal 3 in fig. 3)
The fourth stage is to apply a buffer factor, set at x1.3. The buffer factor allows for the simplicity of the calculation method (eg. not requiring more elusive data such as multiple factory geographical locations and respective energy profiles). Applying a conservative margin to ensure that the GHG calculation does not substantially underestimate a product’s global warming potential (see grand total in fig. 3). A lighting professional can then use this data to perform embodied carbon calculations for their project.
Now the user has calculated the total embodied carbon of a product. CIBSE strongly encourages users to fill out its TM65 reporting form and submit their results, so that it can build a database of products.
The TM65 process: an LED driver manufacturer’s perspective
CIBSE’s intention is that the industry will take the initiative to provide TM65 calculations for MEP products, and publish the figures to the CIBSE database. eldoLED has already started this process: it has performed TM65 calculations for four of its most popular products, with more planned.
As we will see, though, the TM65 process has prompted some new thinking about ways to reduce the global warming potential of the company’s products. This new thinking was accelerated by a request from an eldoLED customer, Stoane Lighting, who provided fixtures for Our Time on Earth, an exhibition at the Barbican with lighting design by Speirs Major, covered in arc #128.
On eldoLED’s part, the TM65 process involved stripping a driver back to its raw materials (see fig. 2), classifying each material type, weighing each, applying the embodied carbon coefficient, and then summing the results. A report page for the 50W SOLOdrive 561/A driver is shown in fig. 3.
Compiling the product data was straightforward. Now eldoLED has a plan to perform TM65 calculations for any of its driver products on request from customers, and for all of its most popular models.
The most interesting insight to emerge from the TM65 process was the overwhelmingly large contribution to embodied emissions contributed by the PCB and the electronic components, as shown by fig. 3. This is prompting eldoLED to rethink its approach to reducing the environmental impact of its products.
We now understand that any reduction in the size and weight of the PCB has a disproportionately beneficial effect on the embodied carbon of a driver product. This is a big challenge for the design engineers at eldoLED. Miniaturisation of electronics systems is not straightforward. For instance, the closer that components are placed on the board, the harder it is to keep them within their maximum temperature limits. The techniques for board size reduction are well understood at eldoLED, and we think we can make some substantial reductions in the embodied carbon in our products over time by reducing the size of the PCB layout.
For a driver manufacturer, power conversion efficiency also has a huge impact on sustainability: the more efficient the driver, the less power is wasted, directly reducing operational CO2 emissions. Increasing efficiency is another long-term project for eldoLED, which is working with customers to balance performance, cost and efficiency.
Alongside these initiatives, eldoLED is in the early stages of investigating the scope to bring driver production closer to the point of end use, and to facilitate re-use and recycling of drivers after their first use. These initiatives are consistent with the principles of a circular economy, and of localisation, both of which have an important role to play in industry’s work to reach net zero.
MEP products in the spotlight
CIBSE’s work in devising the TM65 method, provides a consistent and clear way for the lighting industry to calculate the embodied carbon in the products it relies upon, a valuable tool for the industry to use in reducing its embodied carbon footprint towards zero. Equally important, it is providing information to manufacturers like eldoLED, helping them to understand the sources of embodied carbon in their products, and to use novel design approaches to reduce a product’s carbon footprint.
GreenLight Alliance Reaction:
Mark Ridler, BDP
“TM65 is a start, and a good one, because in the absence of the rigour of EPDs for most of the industry and the punitive cost that they incur to a manufacturer (particularly a small one with a large legacy catalogue), it provides a manageable and meaningful route to embedded carbon declaration. And it is inevitable that this declaration is coming our way, both as manufacturers and designers through European and national regulation and in most likelihood the sustainability evaluators such as BREEAM, LEED, ESTIDAMA etc.
“I have slight reservation about some of the details: the bluntness of the scale up factors about which no designer or manufacturer can influence and accounts for almost half of all lighting declared carbon; the anomalous distinction made between “product” and “building” that means a product with a non-repairable lamp scores better than one with one. But this is minor because the TM is designed to be readily and regularly updated. Fail fast and learn fast, which I support.
“My real misgiving, however, with embedded carbon and lighting is that until we decarbonise the grid in the nation where the luminaire is installed, the carbon in use dwarfs embedded carbon by two orders of magnitude. If you use a bit more aluminium in the heat sink to drive greater longevity or efficiency, then the embedded carbon price is worth paying for the carbon in use benefit. Embedded carbon is already being seen as a driver for the circular economy in lighting and it should not be, because if it is, then throwaway efficient luminaires will prevail as they have since the 90s. The obscenity of the linear economy is in its assault to the biosphere and its insanity in terms of resource depletion. Those should be the drivers of a circular economy.
“So, TM65 is just the beginning. The industry needs to build on this to incorporate full life cycle assessments (LCA) which would drive better evidence-based decisions both in design and manufacture.
“That all said, and if you agree with me or not, the fact that this debate is happening at all is because of visionary manufacturers who are investing in this field and discovering actions they can take in the short and medium term to lessen their/our impact. They are to be applauded.”
Kevan Shaw, EFLA | Kevan Shaw Lighting Design
“It is heartening to see eldoLED beginning to dig into the sometimes confusing world of the circular economy and environmental impact assessments. Given the drift of the climate change discussion firmly anchored on CO2, looking at this through the lens of TM65 is a good starting point. TM65 is very much a simplified broad brush tool to cover the wide spectrum of building services, and doubtless it will spawn more specialised and detailed tools for other building services systems and equipment.
“In the case of eldoLED it has certainly focussed thoughts on future product development by identifying the printed circuit board as the most CO2e intensive element of the product. But this is only a part of the circular economy story. For lighting we now have TM 66* and the associated Circular Economy Assessment Methods for both manufacture (CEAM Make) and design (CEAM Specify) these go much further into the lifetime impacts of lighting products looking beyond the manufacture into the maintainability, repairability, length of service and ultimate recyclability all of which add to the total environmental impact of these products. For lighting this is very important. As mentioned, the focus has been on energy in use as the principle generator of CO2. This is changing quite rapidly, though not equally, in each country. Based in Scotland and focussed on Iceland, both these countries are as near as dammit producing all the electricity they need from non CO2 emitting generating capacity – hydro and geothermal in Iceland, wind, hydro, nuclear and tidal in Scotland. For projects in these countries, and in fact most of the Nordic countries, we need to pay much more attention to all aspects of circular economy.
“In conclusion, well done to eldoLED for taking these issues seriously and incorporating consideration of embodied CO2 in their processes. As specifiers, we need to take the next steps and start asking all our suppliers for information needed to complete our carbon and CEAM Specify assessments for our projects.”
*See arc #124 p.48-50 for an article on TM66
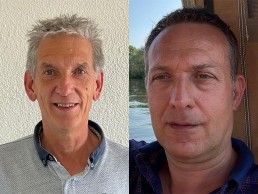